
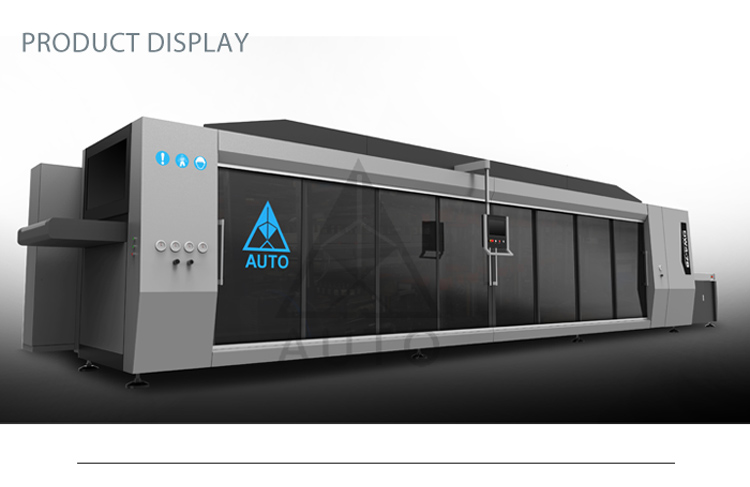
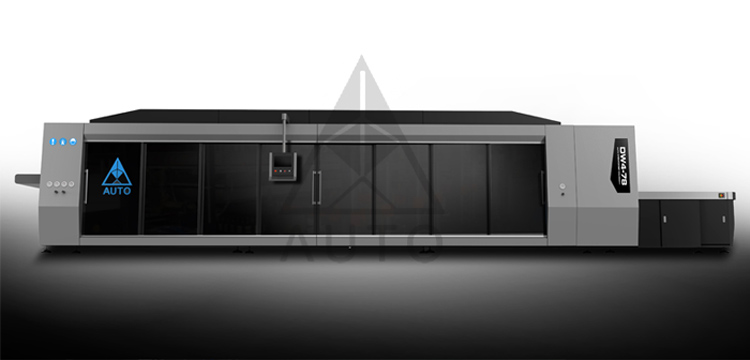
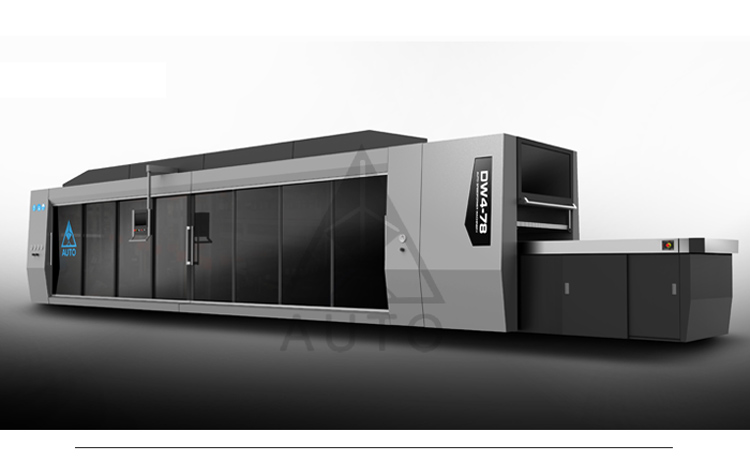
I, Basis Data:
Suitable Material | PP,PS,PET,PVC,BOPS, etc. |
Sheet Width | 390-830mm |
Thickness of Sheet | 0.1-2.0mm |
Max. Formed Area | 800×600mm |
Min. Formed Area | 375×270mm |
Availability Punching Area(Max) | 780×580mm |
Positive formed part height | 150mm |
Negative formed part height | 150mm |
Work Efficiency | ≤50 cycles/min |
Heating Power | 100kw |
Main Motor power | 7.34kw |
Winding Diameter(Max) | Φ1000mm |
Suitable Power | 380V,50Hz |
Air Pressure | 0.6-0.8Mpa |
Air Consumption | 5000-6000L/min |
Water Consumption | 40-45L/min |
Machine Weight | 18,000kg |
Dimension | 16×2.45×3.05m |
Installed Power | 162kw |
II, Summary of Machine
1. DW Multi-step High-speed Thermoforming Machine is our latest developed product imported Germany technology which is the new generation of revolutionary product in the field of packaging, food, electronics industry. This series is widely used and universal. This model can be suit for most of the products as customer requested.
2. High speed, low noise, high reliability, and convenience to maintainance.
3. Max. production speed up to 50 cycles/minute, definitely can be named as high speed thermoforming machine. DW4 type of high speed thermoforming machine can work perfectly for PP, PS, BOPS, PVC, APET, or CPET, due to the advanced automatic servomotor control system.
4. Tool change system of optimized ergonomic design which shortens the time for tool change extremely, together with steel rule cutting station and stacking station, ensure the maximized production time.
5. Advanced heating system with latest modules for temperature control, for fast reaction time, resulting in high efficiency and low production cost.
III, Advantage of Machine
1, Every Station in DW Series is driven by the eccentric crank linkage structure, controlled by Lenze servo motor. Three-guiding-pillars made of superior quality bearing steel Gr15 and hard chromium plating, designs for good rigidity, accurate performance and excellent abrasion resistance, which contributes to the working life of equipment.
2, The Bushing of Crank linkage mechanism is made of superior quality Quenched and Tempered Steel 40Cr, which is imported from Janpan, designs for high rigidity, good resistance of abrasion and pressure, which ensure the working life of 40000 hours.
3, New Designed Heater: Up and bottom all elements use high-temperature aluminum alloy frame design, by weight, low cost, fast heat dissipation, simple appearance. Elstein ceramic heater with the B&R temperature control module ensure the heater steady, high precision and temp control tolerance<1℃.
4, Conveying sheet chain adopted toothed double row roller chain, cooling water inside. Aluminum rails carrying cooling water, a high cooling efficiency in the circulation passage, save water.
5, Low barycenter design, Low height of making cup and steady running performance serves the purpose of human body standing operation and best altitude of observation.
6, Pneumatic control for all the machine set up with SMC components equiped the Parker Air Cylinder, Norgren Solenoid Valve which ensure stability and smooth-action.
7, The whole set of Lenze Automation Control System, makes the high degree automation, accurate control and convenient operation. The touch control operation and document storage function simplifies the operational processes.
8, All the transmission function adopt Lenze Decelerator, which ensure fast reaction, precise length positioning and convenient accommodation for conveying sheet. Servo Decelerator make the feed part easy adjustment and precisely positioning.
9, Thermal Protector for each servo motor, in case of overworking from damaging equipment. And overcurrenct protector for each motor.
10, The adjustment of the unreeling station for sheet rolls, conveyor belt for transport of products, forming station, all is controlled by the Lenze frequency reducer driven.
11, All Bearing is imported from Japan. The high quality of parts increasing life of machine.
12, The max diameter of sheet roll with air device for conveying sheet shelf is 1000mm. The frequency reducer adopt Lenze. Automatic frequency control ensure secondary pollution of products not caused by tabbing sheet.
13, In order to prevent error operating from production process, heater are installed overheat tabbing sheet protection device. Control by Infrared radiation pyrometer.
14, There is alarm function of the sliding doors.
IV, Brands' of Main Electrical Components
Main Parts | Brands |
Control System | B&R |
Station Servo Motor & Reducer | B&R |
Contactor | OMRON |
Encoder | Sick |
Stretching Servo Motor | B&R |
Conveying Sheet Servo Motor | B&R |
Guide Sleeve | Made in Japan |
Axle Bearing | Made in Japan |
Linear Guideway | Hiwin |
Pneumatic Elements | SMC |
Ceramic Infrared Heater | Germany Elstein |
Solenoid Valve | MAC, SMC,NORGREN |
Lubrication System | Lincoln |
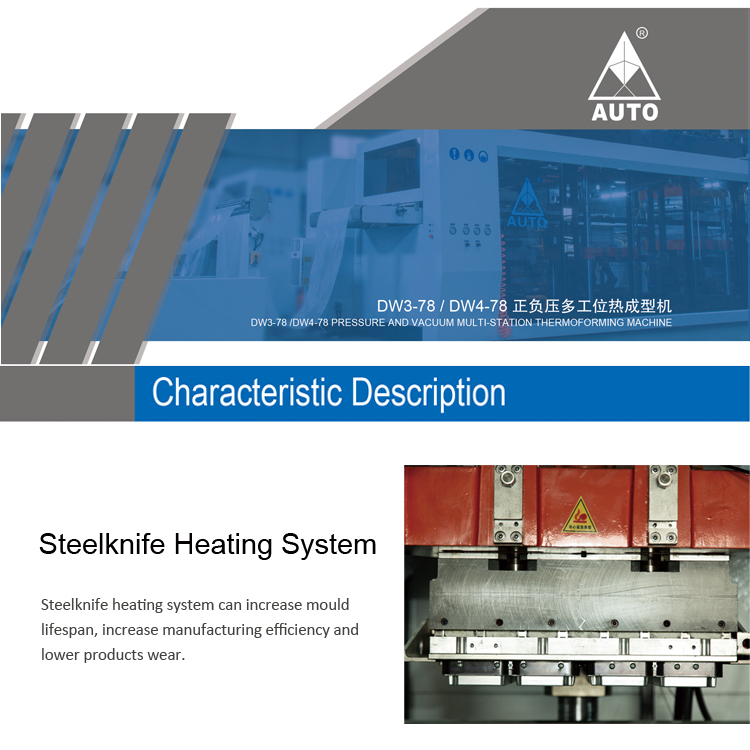
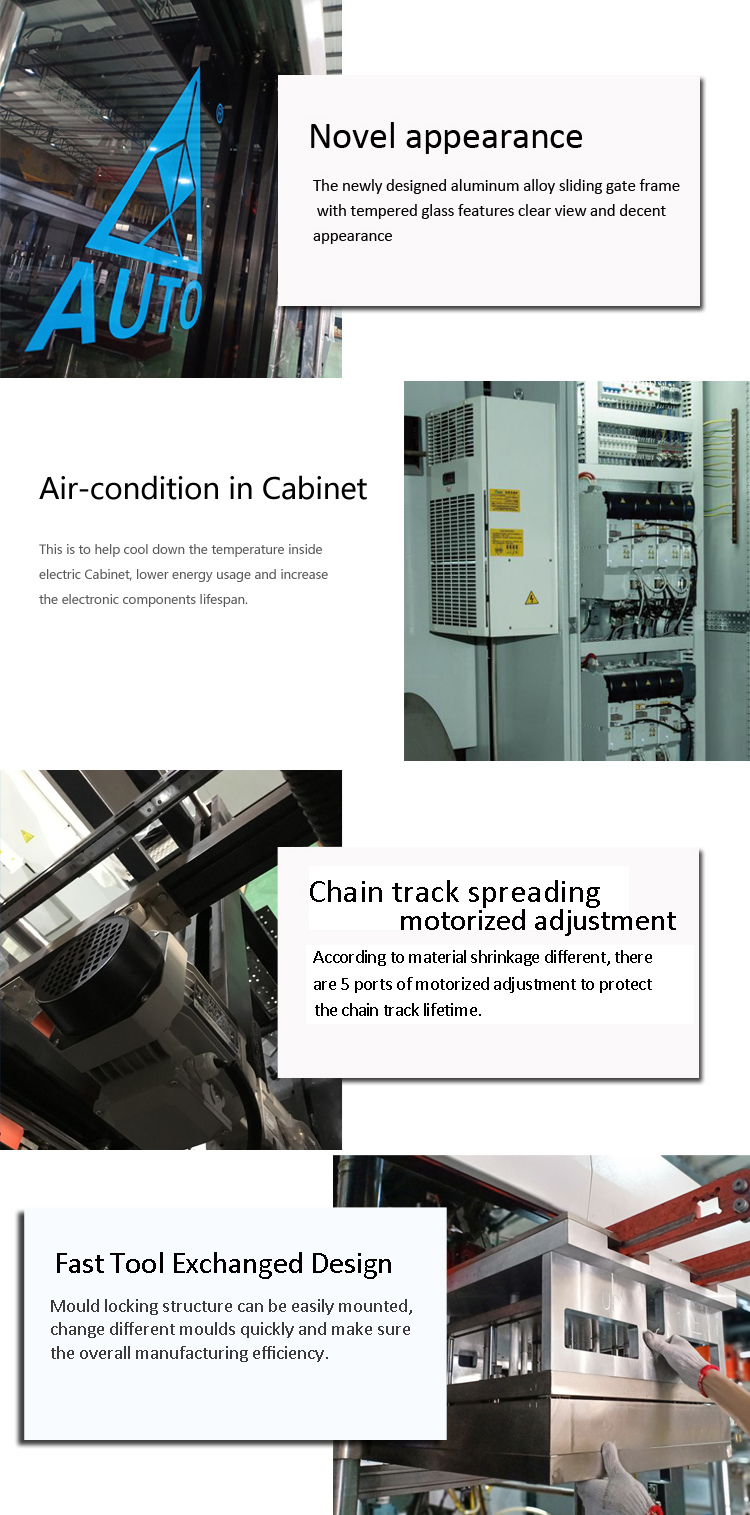
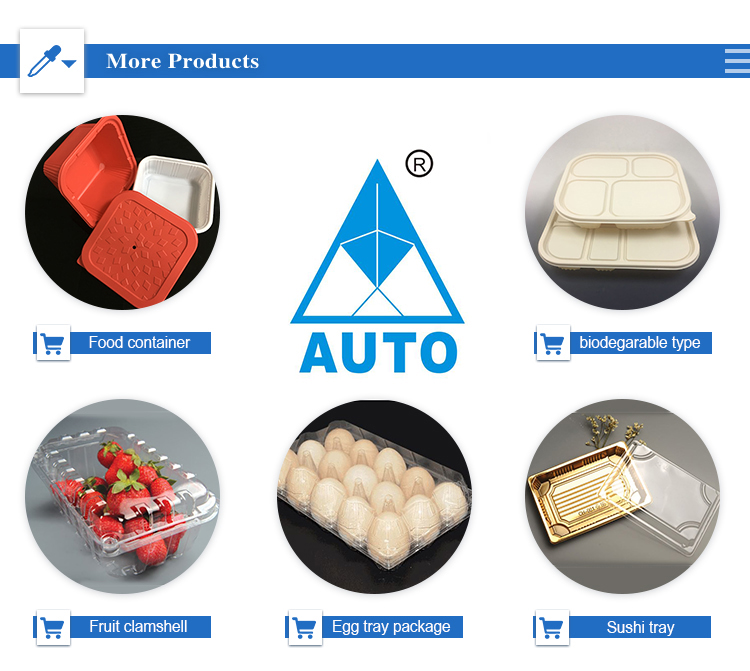
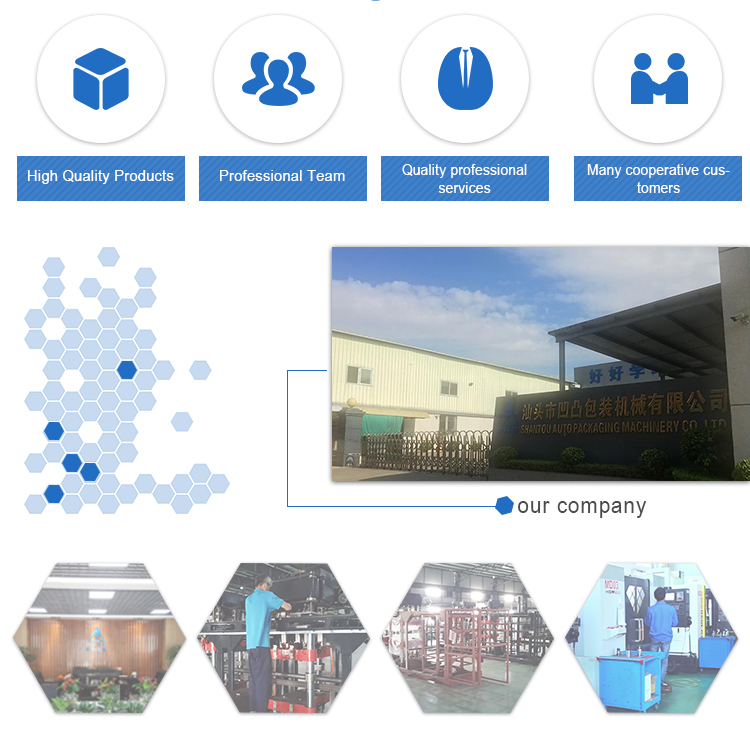
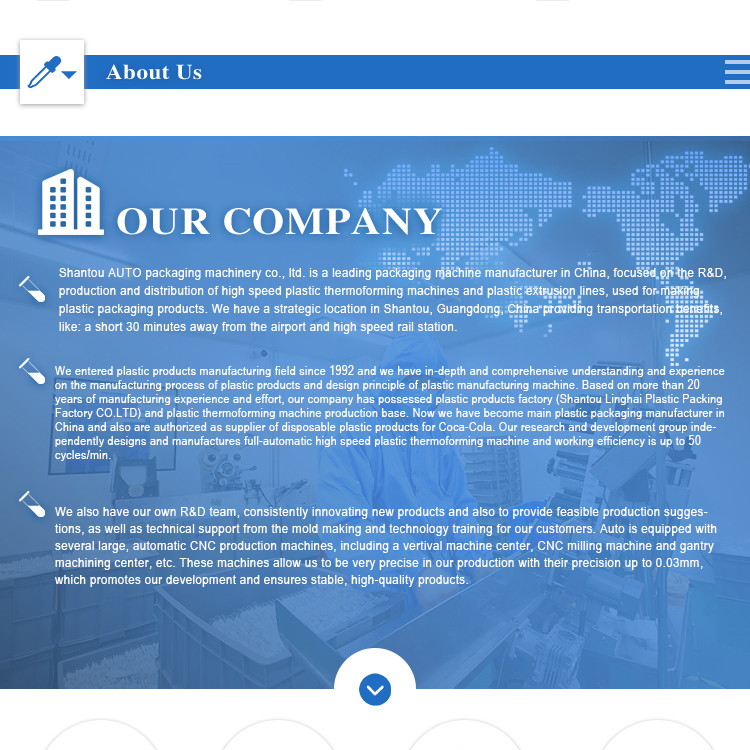