Double piston with elongated mesh continuous screen changer/melt filter for plastic extruder
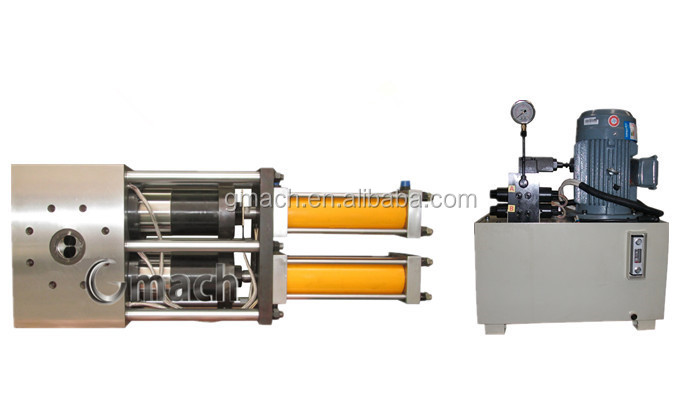
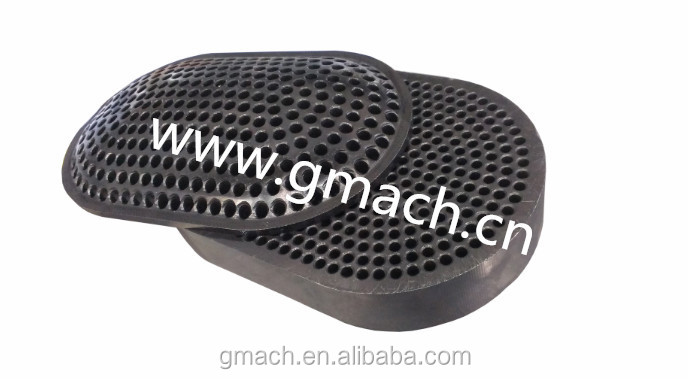
Factory price plastic extruder continuous screen changer melt filter GM-DP-E series is consist of
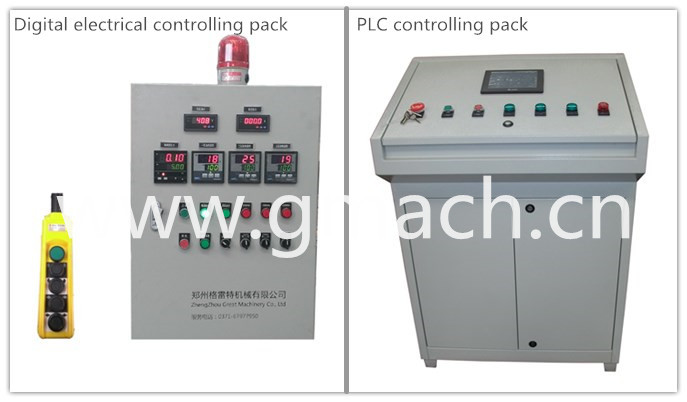
Features of this kind of Double piston with elongated mesh continuous screen changer/melt filter for plastic extruder
Two elongated /oval removable breaker plates on each bearing piston
"Continuous type" means operation of screen change without machine halt or disruption of melt flow.
Equipped with three steps of gas venting system
Fit for almost all kinds of polymers
Flexible installation ways
It works well under the high pressure 400bar(40Mpa) not impact the high performance.
The filtration screen area covers from 56cm² to 520cm², depending on the size, fit for output range from 30kg/h to 1800kg/h.
screen change proces
The screen changer and gas venting process of this kind of factory price continuous screen changer, hydraulic screen changer
one rod is pushed out by hydraulically
the blocked filter screen pack is removed and replaced by a fresh one
the rod is pushed into the housing of the screen changer
the other rods repeat the above steps
The gas venting systen begins to work when the rod is pushed into the housing of the screen changer, and the following picture show the process of gas venting of this type of dual rods continuous extrusion screen changer for polymer melt filtration.
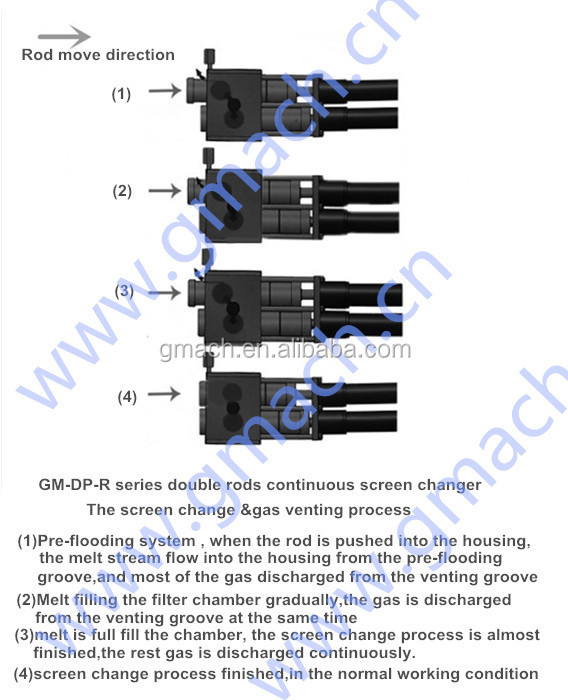
Product show
Double piston with elongated mesh continuous screen changer/melt filter for plastic extruder
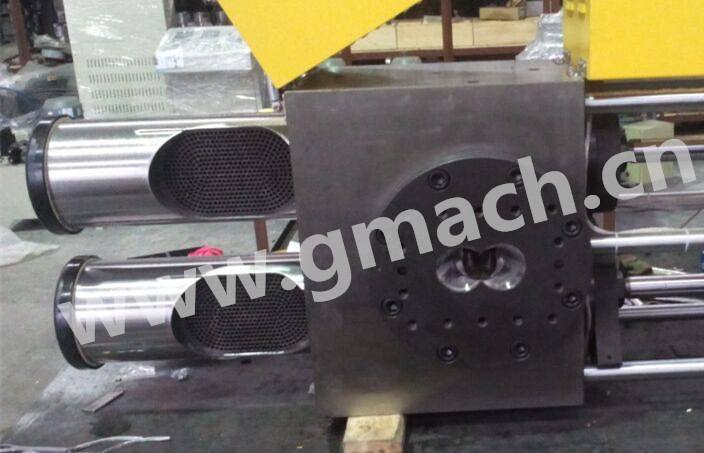
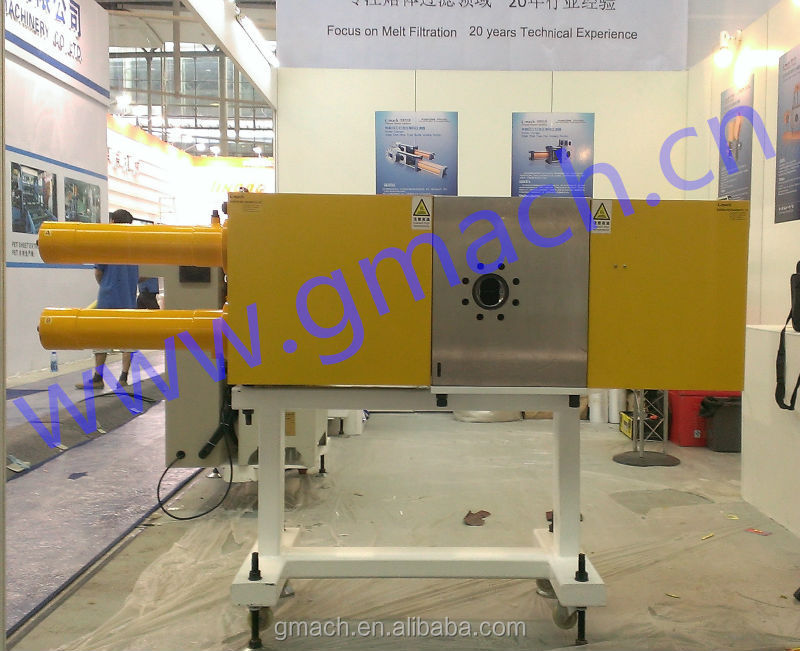
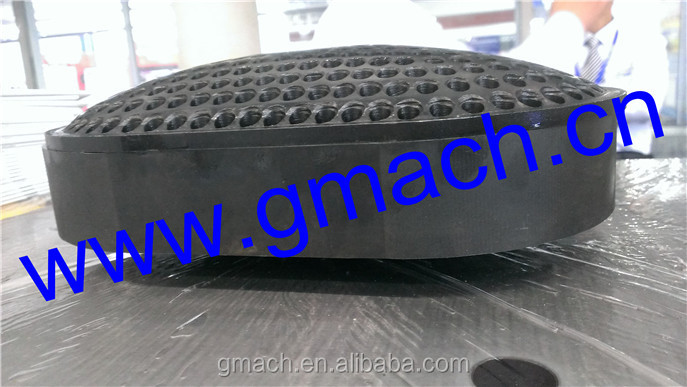
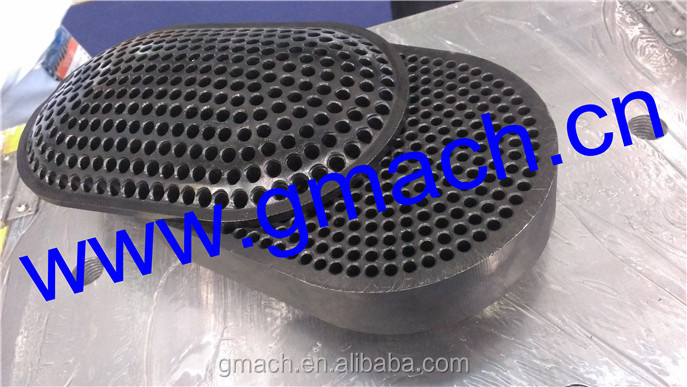
Benifits of Plastic PP under water pelletizing extruson line used double piston continuous screen changer filter
continuous operation
Discharge the gas mixed in the polymer melt by the venting groove
Leak-free mold of operation
Customized design adapters
Flexible installation ways to full use of the limited space
Simply controll by a easy operated control handle
Reasonable price and proved technology
Compare with the GM-DP-R series dual bolts continuous screen changer, the same mode of this two screen changer,this GM-DP-E series screen changer with bigger active filtration area
Main application fields
Cast film (Bubble pack/ Medical/Food Wrap)
Sheet (Foam/Strapping/Plastic cardboard)
Coating (Hot melt adhesive)
Pipe ( Corrugated/Gas Pipe) and profile
Compounding (Master batch/filler)
Wire and cable extrusion
Tubing (Medical/Industrial/Irrigation)
Fibers ( Monofilament/non-woven fabrics)
Pelletizing (strands and water-ring pelletizing)
Recycling of most polymers
Types
Type
| ScreenD&A
| Overall &dimension (mm) | Heating power (KW))
| Output (kg/h)
|
| W*L(mm) | Filtration area(cm²) | L | W | H | L1 |
|
|
GM-DP-E-80 | 60*95 |
| 180 | 170 | 280 | 700 | 2.4/3.2 | 30-180 |
GM-DP-E-100 | 80*128 |
| 220 | 200 | 320 | 810 | 3.5/4.7 | 80-280 |
GM-DP-E-120 | 100*160 |
| 250 | 220 | 360 | 970 | 5.0/7.2 | 220-480 |
GM-DP-E-155 | 130*208 |
| 320 | 270 | 450 | 1100 | 8.2/11.1 | 300-700 |
GM-DP-E-170 | 145*230 |
| 370 | 310 | 480 | 1320 | 9.4/12.7 | 400-1100 |
GM-DP-E-195 | 165*253 |
| 400 | 380 | 550 | 1470 | 10.2/13.8 | 650-1500 |
GM-DP-E-220 | 180*286 |
| 440 | 410 | 590 | 1620 | 13/17.5 | 800-1800 |
Remark:The output rates depend on the individual extrusion process parameters. |
Packaging
Inner packing: bubble wrap film protection
outer packing:wooden case
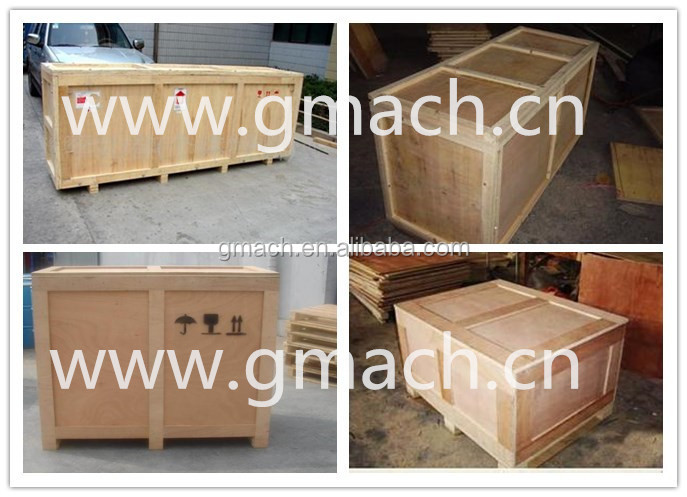
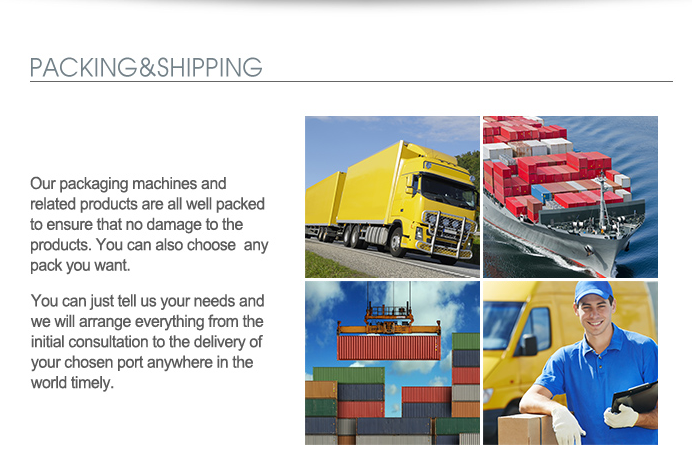
Commissioning
We provide the operation manual for customers to gudie to install the screen changer, and at the requirement of user, salers should send technician to install and commissioning the die at site of Buyers, expenses of the trip should be borne by Buyers.
After-sales service
12 months with proper operation by user, all the spare parts shall be replaced free of charge under guarantee period, fee for transportation and packing will be borne by users.
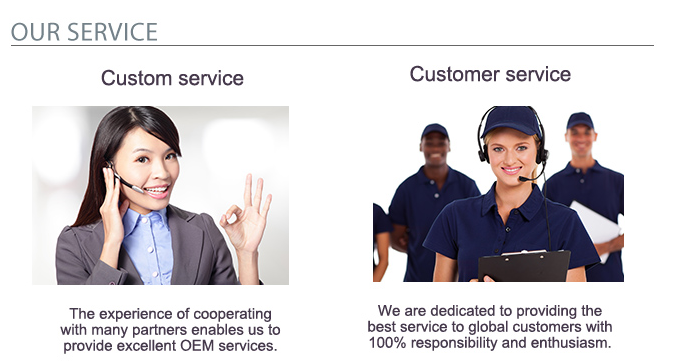